Digitizing supply chain planning processes is a major investment. Here's what a $10b company discovered with their feasibility study.
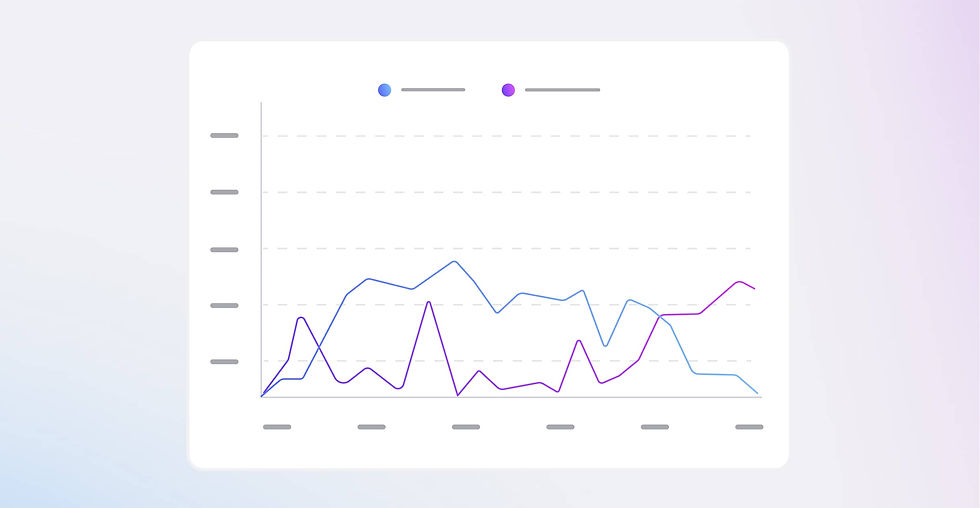
A Multinational Food and Biotechnology Corporation
Revenue: USD 10 BillionPresence: Operates in 36 Countries
Issues Addressed
The organization faced significant challenges that prompted the need for a robust supply chain planning system powered by digital tools. Key objectives included:
Enhancing operational efficiency
Improving planning accuracy
Accelerating decision-making through data-driven simulations
Organizational Challenges
Lack of Integration: Existing demand and supply planning systems operated independently, creating silos.
Excel Dependency: Heavy reliance on manual data updates in MS Excel led to frequent human errors.
Limited Forecasting Methods: Minimal use of statistical forecasting hindered forecast accuracy.
High Workload: Operations and planning teams faced excessive workloads, reducing productivity.
Absence of Scenario-Based Decision-Making: Decision-making lacked flexibility and scenario-based capabilities.
Transformation Solutions
During the consulting phase, the organization embarked on a transformative journey in Sales & Operations Planning (S&OP), addressing gaps and operational inefficiencies. Key steps included:
Comprehensive Business Study: Conducted an in-depth analysis of current processes in collaboration with each department.
Stakeholder Engagement: Engaged key stakeholders from Sales, Demand Planning, Production, Procurement, Finance, and IT.
Critical Review: Evaluated critical business elements, including people, processes, data, and systems.
Goal Definition: Defined the organization's current state, challenges, opportunities, and new goals.
Improvement Areas: Pinpointed core areas needing enhancement to create a responsive supply chain and planning process.
Achieved Results
Process Optimization: Documented and implemented process improvements that delivered tangible business value.
Stakeholder Alignment: Aligned recommendations with key stakeholders and business owners to ensure shared understanding and buy-in.
To-Be Recommendations: Designed future-state processes, including:
ROI Tracker
Proposed IT Landscape
Revamped Supply Chain Planning Processes
This transformation addressed the organization's challenges while laying the foundation for an agile, efficient, and data-driven supply chain framework.
Comments